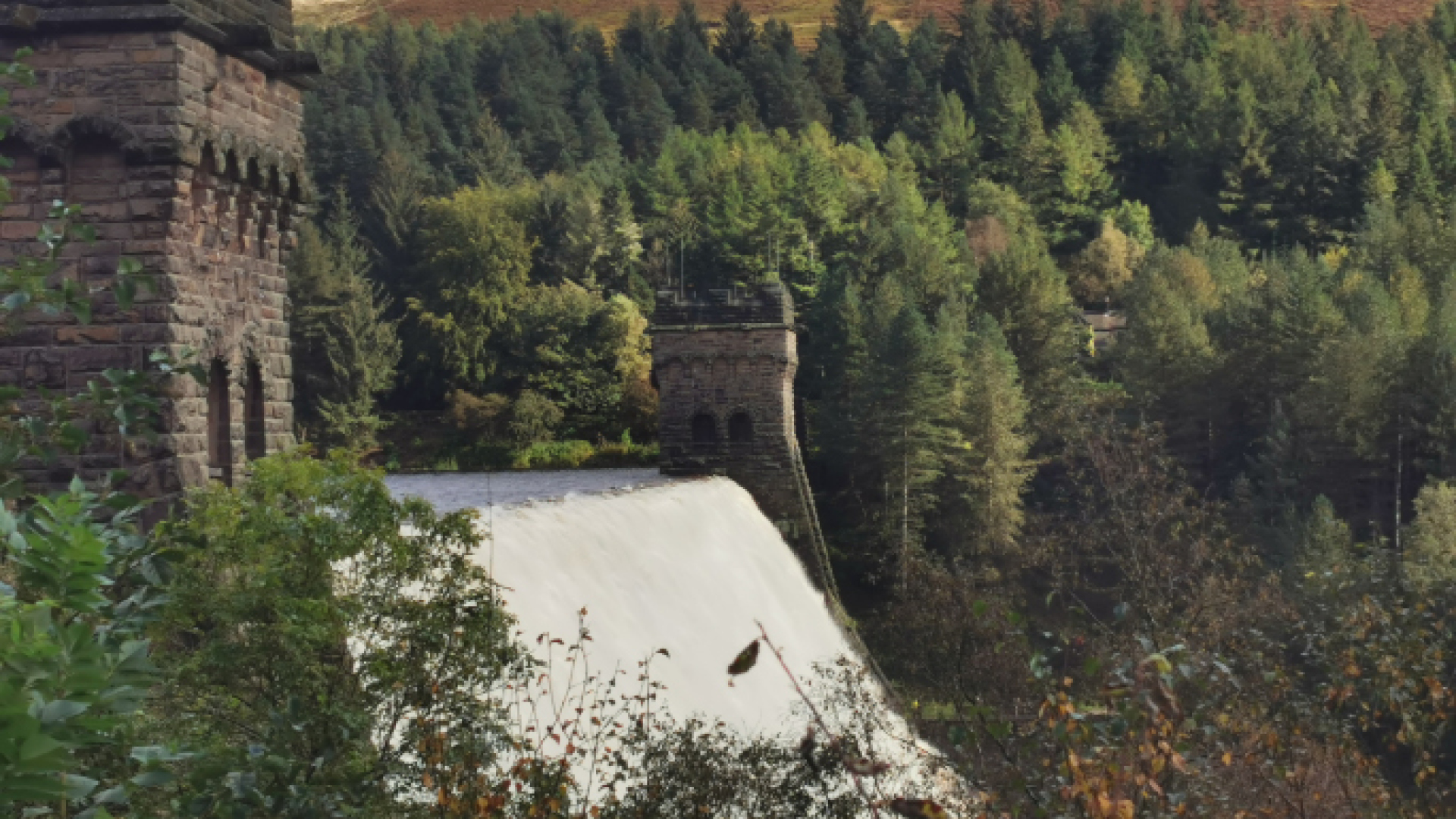
Glenfield Invicta Provide Solution for Challenging Installation
The ability to quickly and safely perform reservoir drawdown can be crucial to the protection and preservation of a dam.
Damflask Reservoir is located in the Loxley Valley, 5 miles to the west of Sheffield. Completed in 1895, Damflask is one of four reservoirs built at that time to supply water to both the local population and the heavy industries for which Sheffield was famous. Damflask features an earth embankment dam with a clay core, a design often referred to as a ‘Pennine embankment' type.
Scour Pipeline
Like most dams, Damflask has a scour pipeline that runs through the bottom of the dam wall.
The scour pipeline has two principal functions. It can be used to flush out sediment that has built up behind the wall, and it can be used to quickly draw down water from the reservoir if, for example, the dam is damaged.
Insufficient Capacity
Yorkshire Water identified that the scour pipe capacity at Damflask was inadequate to meet its 1 million litres per day draw-down target. MacDonald Bentley (MMB) was appointed to devise and implement a solution.
Increasing Flow Capacity
The proposed approach was to replace the existing DN457 cast iron scour pipe with a much larger DN900 ductile iron pipe to increase flow capacity by a factor of 6.
The existing manual flow control valve was located within the scour tunnel and only accessible under confined spaces working. It was decided to site the new flow control valve at the scour pipe outlet.
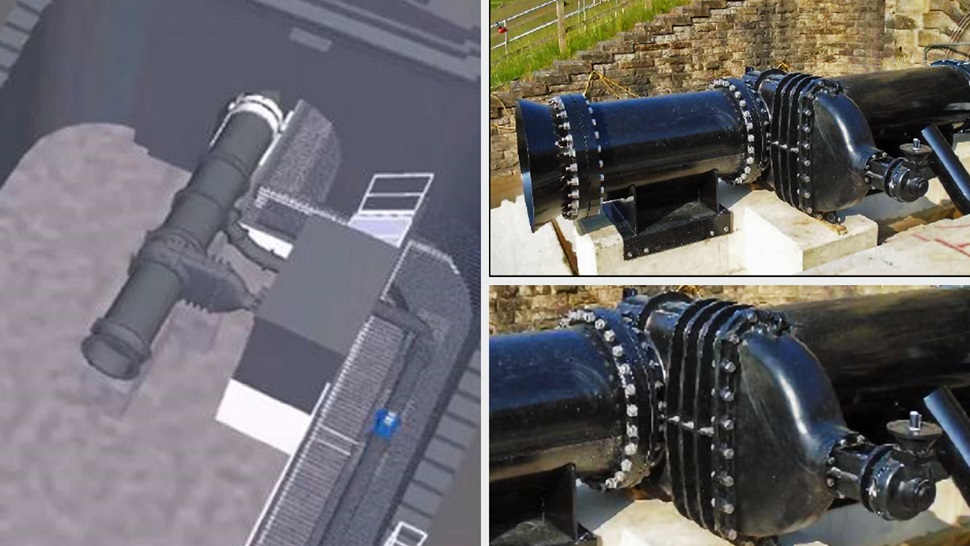
The images above show the 3D render installation and the finished installation with the valve.
Glenfield Invicta Specify Optimal Solution
MMB consulted with Glenfield Invicta as to the type of valve to be used. Free discharge valves were considered because of the high flow velocities; free discharge valves are ideal for controlling flow rates and managing energy dissipation. In the case of Damflask, however, flow control was deemed not to be a determining factor and Glenfield Invicta proposed a DN900 AVK Series 54 reservoir specification gate valve, designed to meet the discharge specification of 6m ³/s.
Automated Control
Control of the valve was to be automated and Glenfield Invicta supplied the electrical actuator and designed a bespoke extension spindle to connect the bevel gearbox to the actuator. Both the actuator and extension spindle were fitted on site by Glenfield Invicta engineers.
Sideways Challenge
The configuration of the site, with the actuator and other control systems located in a kiosk near the pipe outlet, required that the gate valve be installed on its side. A standard gate valve of this size installed on its side would typically experience operational issues due to accelerated wear and tear between the body and the wedge, the increase in operating torque required due to the friction of moving parts, and potential misalignment issues. The design of Glenfield Invicta’s reservoir specification
gate valve, developed with input from Yorkshire Water, incorporates several features that overcome these challenges. These are outlined below:
Aluminium bronze shoes and channels
Aluminium bronze shoes and channels result in a very tight and continuous tolerance between the body and wedge throughout the valve stroke. This reduces potential vibration and fatigue damage. It also reduces bearing stresses on the contact areas as well as improving the alignment and sealing performance of the valve. Operational torque requirements are lower due to the reduced friction coefficients.
Jacking screw
The addition of a jacking screw (or two on larger sizes) at the base of the valve allows a direct axial thrust to be applied to the base of the wedge. If the valve has been closed for long periods of time, it can become increasingly difficult to operate. Rotating the jacking screw ‘pushes’ the base of the wedge up a small distance, sufficient to ‘crack’ the valve out of its seated position; normal operation of the valve from the valve stem can then be carried out with ease. The jacking screw also acts as a mechanical stop which prevents over-travel of the wedge which can cause considerable operational issues with metal seated gate valves.
Stainless steel fasteners and stem.
Stainless steel fasteners and stem, and an increase in coating thickness, combine to prevent corrosion and increase the valve’s operating life.
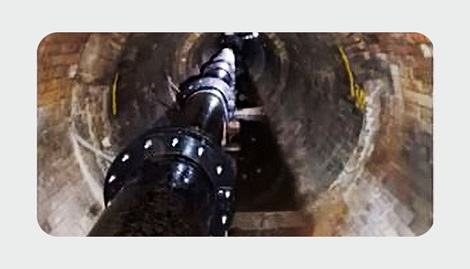
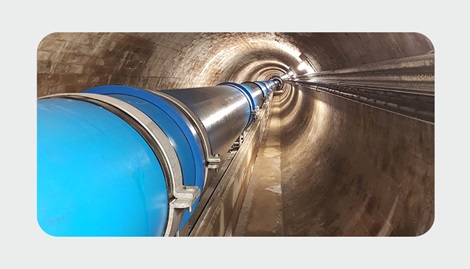
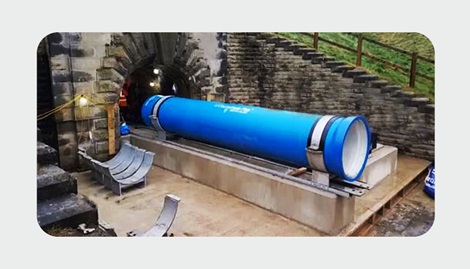
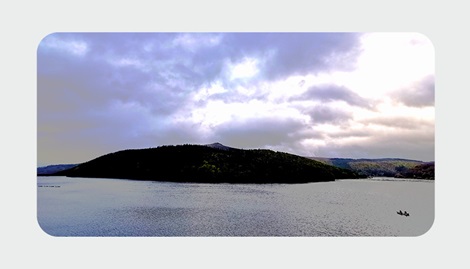
‘Damflask was a really interesting project to work on, and MMB deserve great credit for their creativity in overcoming significant access and engineering challenges on site.
For example, there was initially no functional access to the pipe outlet and a temporary haul road had to be created and pad constructed for a crawler crane. The crane lowered the gate valve down to the site of the pipe outlet.
The development of the reservoir specification gate valve has proved a great success. They have now been used on many other UK and international projects including the supply of a DN1600 Series 54 on Gouthwaite reservoir in North Yorkshire at about the same time as the Damflask project."
It is just one of many examples of Glenfield Invicta listening to customers and working with them to engineer solutions to the challenges they face.’
Contact Greg Morris our, Dams, Reservoirs & Hydripower Specialist, who can give advice on your project, product selection and training, at one of our UK manufacturing site or at your premises. Greg's phone number is shown above.