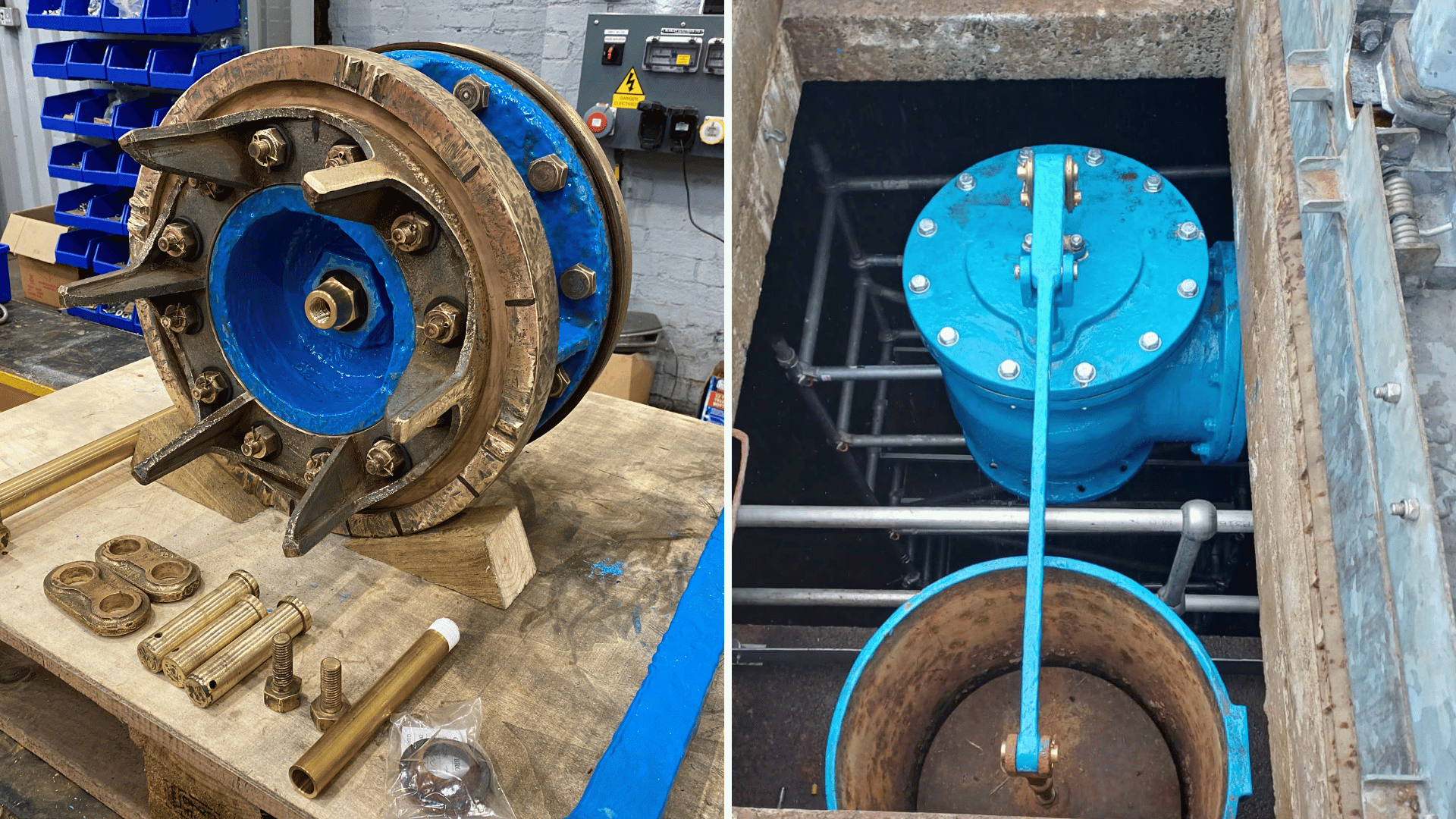
Glenfield Invicta has refurbished and reinstalled the internal workings of the float valve at Parkhead DSR in Falkirk. Refurbishing the valve ensured the reservoir was back in service as quickly as possible, as well as delivering a positive sustainability impact, and reducing costs.
Parkhead DSR is located in Falkirk. Typical of many DSR, Parkhead is essentially a large buried concrete chamber. The float valve in the chamber, similar to a larger version of the ball valve found in many domestic cisterns, was allowing water to pass when it was in the closed position. George Leslie, the Scottish Water framework contractor working on the reservoir, commissioned Glenfield Invicta to dismantle and remove the internal workings of the float valve, and to provide a condition report and recommendations.
The valve was inspected in Glenfield Invicta’s Kilmarnock workshops
The Parkhead float valve was stripped down to its individual components by Glenfield Invicta engineers in its Kilmarnock workshops. The components were cleaned and then subjected to a detailed visual inspection.
The inspection determined that the core valve casting was in reasonable condition, as were the bronze fastenings located within the valve. However, the bronze centre shaft was found to be bent, The valve’s lever arm was badly corroded with a slight bend. Both the gaskets and seals were worn and damaged, contributing to the poor in-situ performance of the valve.
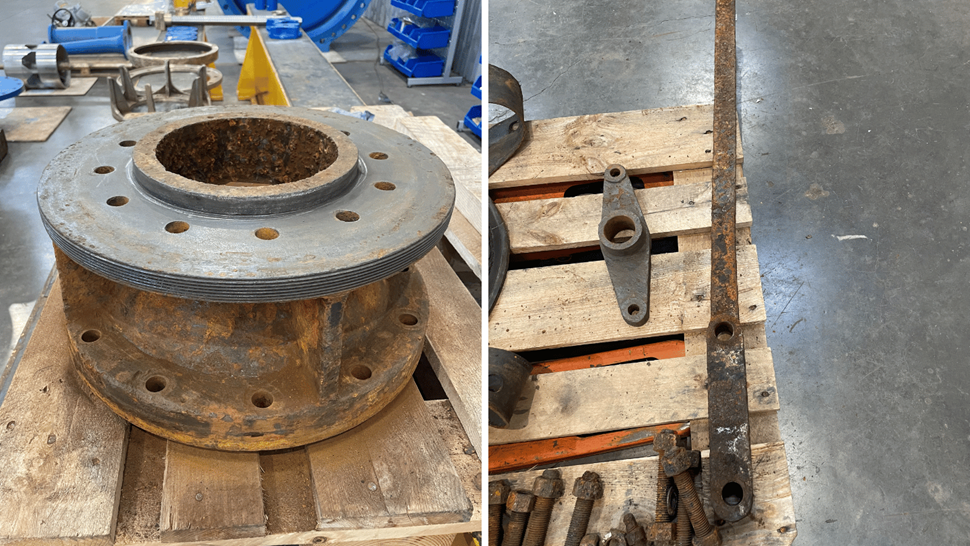
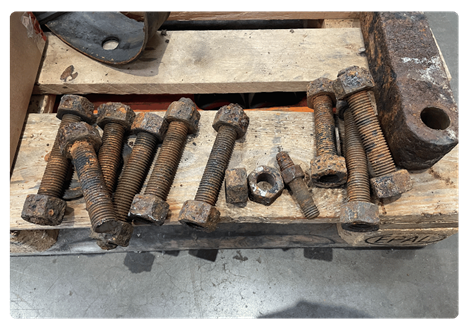
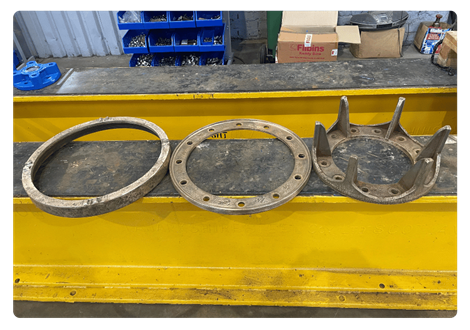
Glenfield Invicta engineers proposed that the valve be refurbished and reinstalled
Based on the results of the inspection, Glenfield Invicta proposed that the optimal course of action was to refurbish the internal workings of the valve and then to reinstall. Refurbishing and reusing the existing valve was more economic than supplying a new valve, was better from a sustainability perspective, and ensured the function and performance of the DSR remained as it was when it was first built. The process was also quicker than procuring a new valve.
The valve centre casting was shotblasted and coated with a WRAS Approved paint. The slight bend in the lever arm was determined to have no impact on valve performance and this was also shotblasted and coated. A replacement bronze valve shaft was reverse engineered, as were the seals and the gaskets. Due to heavy corrosion, the legacy valve cover fasteners were replaced with new.
Reverse Engineering
When standard replacement components or legacy drawings are unavailable, components may be ‘reverse engineered’. Reverse engineering can be defined as, ‘The process of analysing and understanding the design, structure and functionality of a product by working backwards from its final form’.
At Glenfield Invicta, after breaking down a valve or other product to its core components, it may be found that one of more of the components may no longer be fit for purpose. For example, a component may be found to be worn, misshapen, have stress corrosion cracking and so on. In such cases, Glenfield Invicta’s engineers will reverse engineer the component by studying its function, the material(s) used, and its features and dimensions. Once the engineers have sufficient accurate data, they will create detailed technical drawings from which a replacement component can be manufactured.
From a materials perspective, unless there are compelling reasons otherwise, the reverse-engineered component will be manufactured from the same material on a like-for-like basis. This ensures the function and performance of the valve remains the same as when it was first manufactured.
In some cases, for example where there is no current equivalent, a complete valve, including castings, may be reverse engineered.
Glenfield Invicta engineers returned to the Parkhead DSR to reinstall the internal workings of the valve, and to undertake tests to ensure it was functioning correctly.
Jim McAllister led the Glenfield Invicta project team
"Refurbishing valves, such as the Parkhead DSR float valve, is extremely rewarding for all involved. Not only are we preserving what are, in my eyes at least, industrial works of art, but we are also playing our part in minimising the environmental impact of the works at Parkhead. In many cases we have original technical drawings from when a valve was first designed and manufactured in our archive."
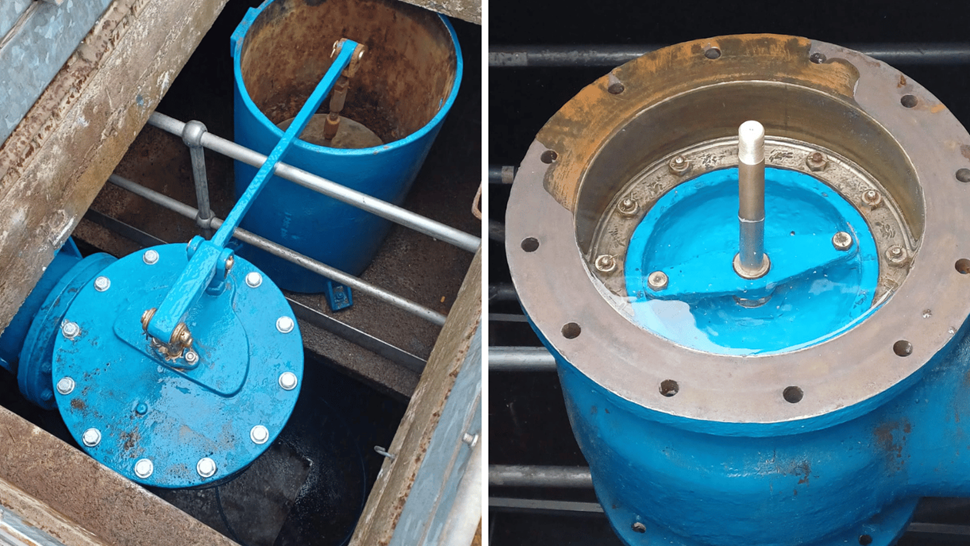