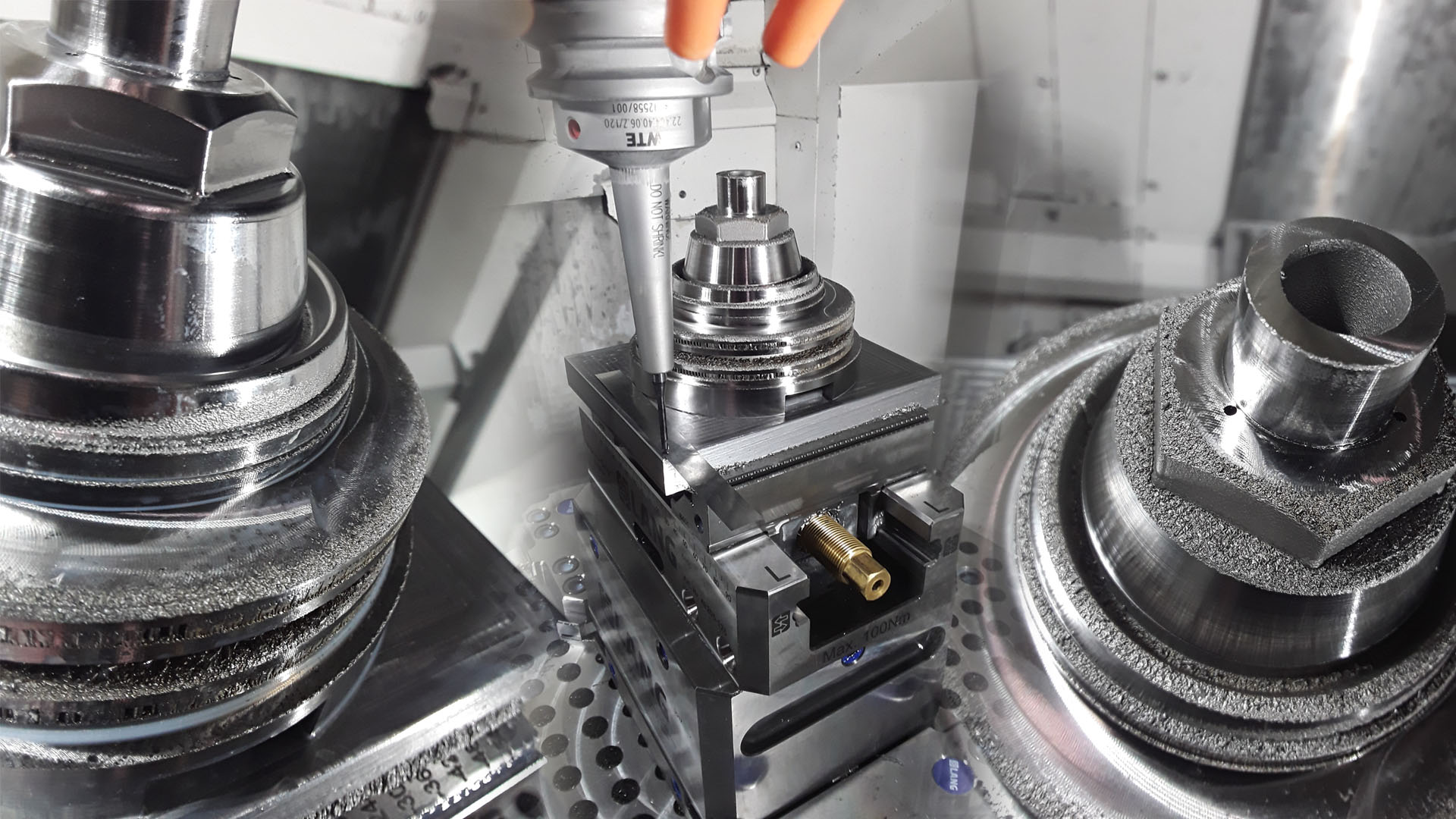
Greater control in production and higher quality with metal 3D printing
3D printing technology has helped produce a part where machining is unnecessary, given us complete control over our process and increased the quality. 28-10-2024
Innovation is essential to AVK & Glenfield Invicta and is one of our five core values that act as our guiding principles and set the direction for how we run our business. We focus on innovation and development of new and optimised products of high quality and with a long lifespan.
Our innovative approach ensures we adapt our designs and solutions to address both current and future challenges, particularly in critical water and wastewater applications.
“The product we looked at regarding 3D printing is the service valve serie 16 POM valve. It is a product used for service outlets towards end customers, running on the shorter pipe lengths in the supply that go directly to the customers,” says Tonny Sprogø, Product Manager, AVK International A/S.
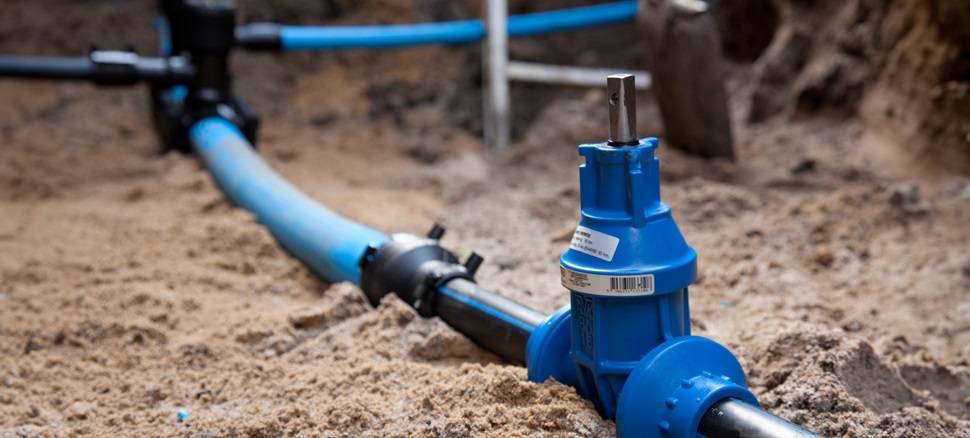
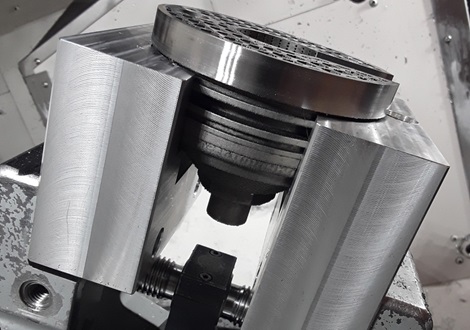
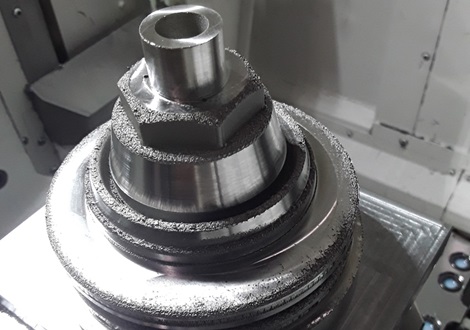
There was a lot of machining of the top of this product which we believed should be unnecessary. So that was the challenge we needed to solve.
“3D printing technology has helped us solve the challenge of producing a part that is precise enough that machining is not necessary. Being able to avoid machining means we avoid a lot of clamping in production where you have to take into account the variance of the parts. And furthermore, it actually also allows us to start automating some more processes,” says Michael Mortensen, R&D Manager, AVK Holding A/S.
Better injection moulding with 3D printed tools
The component we have used 3D printing for in this case is an internal structure in a larger injection moulding tool, which ends up injection moulding a part that has a critical internal structure. And it is the entire inner core of this critical internal structure we have chosen to 3D print. The 3D print is produced by the Danish Technological Institute.
“We have used 3D printing in our moulding tool, where we knew that we would face some challenges with cooling in the tool. There is very little space in the part. We inject internally to get the right part quality, and it is very important that we control the temperature precisely in that area,” explains Bo Eric Jacobsen, Manager Project and Tooling, AVK Plast A/S. AVK Plast A/S primarily deals with injection moulding and supply parts internally for AVK’s products, mainly valves.
Because we have so little space, 3D printing can help us make some cooling channels exactly where we need them to be as well as channels for sensors, so we have complete control over the temperature, where it is most important to get the right part quality.
“The reason we chose to use 3D printing for this specific component is that there are some challenges, where we need to place an inlet inside the part, and that function means that we end up struggling with some energy that we can’t remove without having a cooling system located inside the block. So, we need a cooling function between some heat and some external part, which we would not be able to create in any other way than by using 3D printing,” explains Nils Paaske, Tooling Engineer, AVK Holding A/S and adds:
“In the design phase, we have tried to think out of the box, because when we 3D print, we can create all kinds of cavities that we normally can’t produce. So, 3D printing is brilliant in this case.”
To regulate the temperature, the core was designed with built-in cooling channels running like a metro system under the part's surface. These channels allow us to blow cold air through the part, lowering the temperature. Additionally, an insulating layer surrounds the central inlet where the hot plastic flows, ensuring that the plastic in the inlet does not cool and solidify before reaching the mould.

Easing processes today – Influencing tomorrow
By means of 3D printing we can now control the heat development in the tool, we have complete control over the process and, in the end, we achieve a higher quality.
In the future, it is likely that a larger amount of the technical internals in an injection moulding tool will be 3D printed, as it is gradually becoming price competitive, because you get more details.